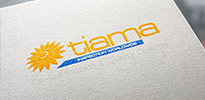
Tiama HOT form, a new sensor at the hot end
A compact and innovative system
The main feature of the Tiama HOT form is to measure the infrared emissivity of articles. This is a key information that allows operators to detect glass repartition issues or temperature issues at the early stage of the process, before containers reach the cold end. In order to do that, the system has to be equipped with one infrared camera (a second camera can be proposed as an option) located in the lower part of a metallic tube to be protected from the heat of articles on the conveyor. And to ensure a full cooling of the system, this tube is air-cooled thanks to a vortex system.
[…]
The Tiama HOT form is synchronized with the IS machine. This enables to link the images and the statistics provided by the system to the sections and cavities of the IS machine. Plus, when the system detects a defect on a container it can also reject it immediately.
The Tiama HOT form uses the latest generation of infrared cameras. It measures the radiation of containers on the conveyor which gives information on glass repartition. Thanks to this, the system is able to detect defects such as thin glass which may indicate a problem with blank mold cooling or with glass temperature. The system also provides right/left asymmetries measurements of articles. For example, this information helps to detect wedge bottom which may be caused by a bad loading (not central) in the blank mold. The Tiama HOT form also delivers statistics to highlight sections or cavities with problems in order to help operators preventing the creation of defects. These statistics are given by zones on the container. Indeed, during the machine setup, the user cuts articles into several areas. The user can then track cautiously the statistics on specific areas based with recurring issues.
This is an extract of an article published in a magazine. To read the entire article click here.